Our long history with coiling stainless steel wire laid the foundation for our success with nitinol. To serve the ever changing needs of the industry, CWT has invested in dedicated equipment to its nitinol coil manufacturing line.
Increasing demand from top OEMs to diversify their product portfolios has required CWT to overcome manufacturing challenges associated with nickel titanium. Our engineering team’s ability to quickly produce samples and prototypes helps innovative startups fast track new product development.
- Nitinol coils made from round or flat wire
- Wire as small as 0.0008” in OD or thickness
- Computer-controlled parameters for pitch, length, and tension
- Custom shaped Nitinol wireforms and assemblies
- Full machine shop for custom fixture manufacturing
- Nitinol core wires with ground tapers and profiles
- Starting wire sizes as small as 0.005” OD up to 0.125” OD
- Nitinol k-wires and pins with threads and sharp tips
- Custom sized and shaped mandrels produced in-house
- Capable to use all grades and finishes of Nickel Titanium
Custom Nitinol Coiling
CWT provides customized medical wire coiling solutions that meet or exceed design requirements needed by the top OEMs in the medical device industry.
Custom Nitinol K-Wires
With the ability to grind various geometries, our ability to manufacture orthopedic wires is unique. From K-wires (Kirschner wires), Steinmann pins, or fixation devices, CWT can help custom manufacture your medical component for you.
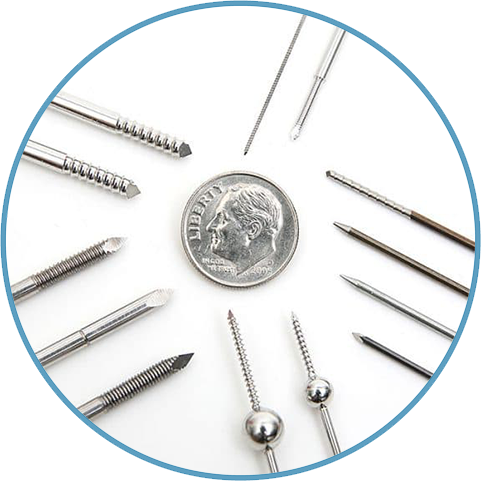
Nitinol Grinding
CWT offers medical grinding capabilities to manufacture guide wires, core wires, mandrels, hypotubes, K-Wires, orthopedic pins, needle prototypes, and components.
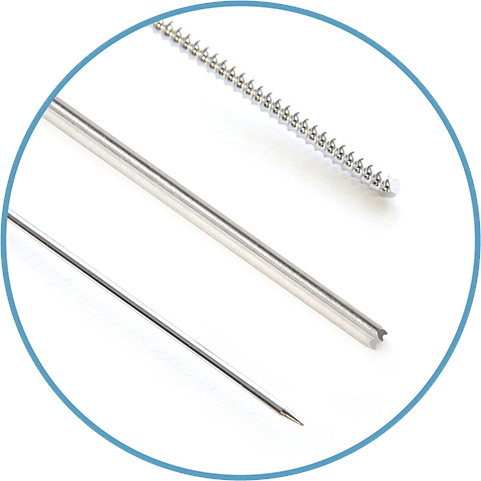
Nitinol Shape Setting
CWT specializes in custom wireforms and components made from precision round or flat wire for medical, dental, and surgical device manufacturers. Laser and plasma welding services can be utilized to provide complete assemblies.
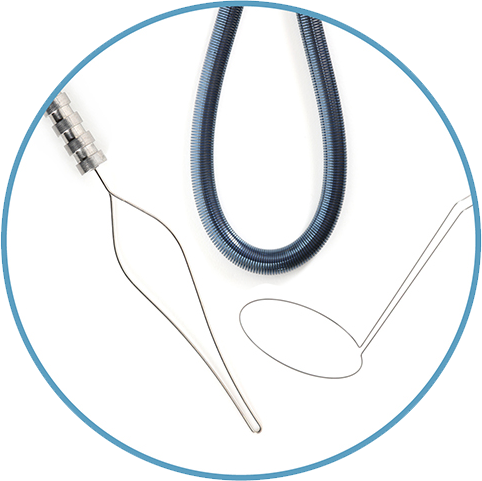
When your deadline is down to the wire, choose CWT.
"*" indicates required fields