Versatility in Laser Marking
Lasers have been used in manufacturing since 1965, when Western Electric created the first laser to drill holes in diamond dies. Over the years, companies have continued to use lasers for more and more tasks that require great precision, such as cutting and ablation. In the 1980s and 1990s, these companies integrated computers into laser marking systems that are able to create tiny identifiers on a variety of surfaces, including metal. Now, laser marking is widely used in many different industries to differentiate parts, mark company logos, add depth bands, and accomplish any other engraving capabilities that companies wish.
How Laser Marking Works
Laser marking creates impressions through high-energy pulses causing the material to melt creating a black, grey, or white marking. During this process, the material both heats up and cools down within milliseconds. In that time, the surface roughness changes, which creates permanent markings.
Laser Marking in the Medical Industry
In the medical industry, it is very important to differentiate parts from one another due to the high emphasis on quality control. Tracking surgical device quality is easier to accomplish when each component is clearly marked with a lot, batch, or part numbers. As demand for medical components has increased, medical OEMs rely more heavily on a system that marks and tracks every traceable step in the component manufacturing process, allowing them to easily determine the source of a defect if one arises.
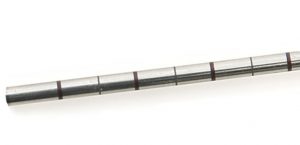
Depth markings can be set at any distance required by the specifications for usage
Depth Markings
When doctors and other medical staff are using surgical components, they may need those components to clearly show depth to ensure accuracy. That is where depth markings come in. Laser marking can create precise depth markers on components to ensure they are placed at exactly the right location. Even a millimeter of discrepancy can result in product failure, which is why there is no room for error in the marking process. Additionally, it is imperative that the marking be permanent, and not fade or corrode over time.
Advantages of Laser Marking
While this technique of marking components does require specialized equipment, it can be advantageous for several reasons:
- It does not require a flat surface to function. Laser marking is equally effective on both flat and shaped surfaces, which is why it works so well for medical device components such as guide wires, k-wires, and pins.
- It is fast and efficient. Machines can have writing speeds of up to 2,500 mm/sec.
- It is permanent. The only way to remove the mark is by scratching off layers of the substrate to make visibility difficult. Therefore, medical professionals need not worry that cleaning, sterilization, or other procedures will cause any significant damage to the image.
- It is easily customizable. Because the machines use computer software to create the image, code, letters, numbers, or other markings, it’s a simple process to make changes depending on what the customer needs. Additionally, manufacturers who have experience with laser marking can advise customers on what colors and contrast levels would work best for their products.
- Marks have a high resolution. Resolution can be as high as 1,000 dpi for a text that is as small as .5 mm. This makes it much easier for end-users to read without having to squint or use a magnifying glass.
Ultimately, laser marking is the easiest—and most accurate—way to create permanent marks on the surface of medical device components. Medical device manufacturers need a process they can count on to properly identify and categorize components of machines. This is particularly important when ensuring quality control—they can quickly and easily isolate any parts that came from the same batch. When sourcing a laser marking company, manufacturers should look for entities that are able to provide a seamless process from start to finish.